Rompiendo récords: nuestros depósitos de agua de lluvia XXL
Hasta 13 metros de largo con un volumen de 52.000 litros: Las cosas realmente grandes se fabrican en nuestra nueva planta de Neuried. El director de la planta, Heiko Rapp, nos lleva al interior de las instalaciones de producción y nos explica cómo se fabrican los depósitos de agua de lluvia XXL...
Vamos allá. Pero, ¿por dónde empezamos? Heiko Rapp nos lleva al exterior, donde acaba de llegar un camión procedente de la cercana Herbolzheim. Allí, en el Centro de Competencia de Materias Primas GRAF, se reciclan plásticos a partir de residuos, del contenedor amarillo.
Llegan a Neuried y a los demás centros de producción de GRAF en Teningen y Dachstein como granulado y se transportan primero a enormes silos. Pero antes de dar forma a los plásticos de alta calidad, hay que molerlos en un enorme molino.
La energía para la producción procede en gran medida de fuentes sostenibles, explica Heiko Rapp. En el tejado, por ejemplo, hay un enorme sistema fotovoltaico que cubre por sí solo el 70% de las necesidades de electricidad, e incluso el 100% durante el día.
Pero ahora volvemos a nuestro tanque y a nuestro pequeño tour. Un nuevo molde para un depósito plano platin se está llenando con el polvo de plástico. «Es como un molde de tarta gigante», explica Heiko Rapp. Convenientemente, el horno en el que se coloca la cáscara finalmente cerrada ya está precalentado... A 300 grados, el plástico del interior del molde se Y finalmente se distribuye de forma uniforme gracias a los lentos movimientos de rotación de la máquina. La pared exterior del depósito se acumula en la pared interior del molde.
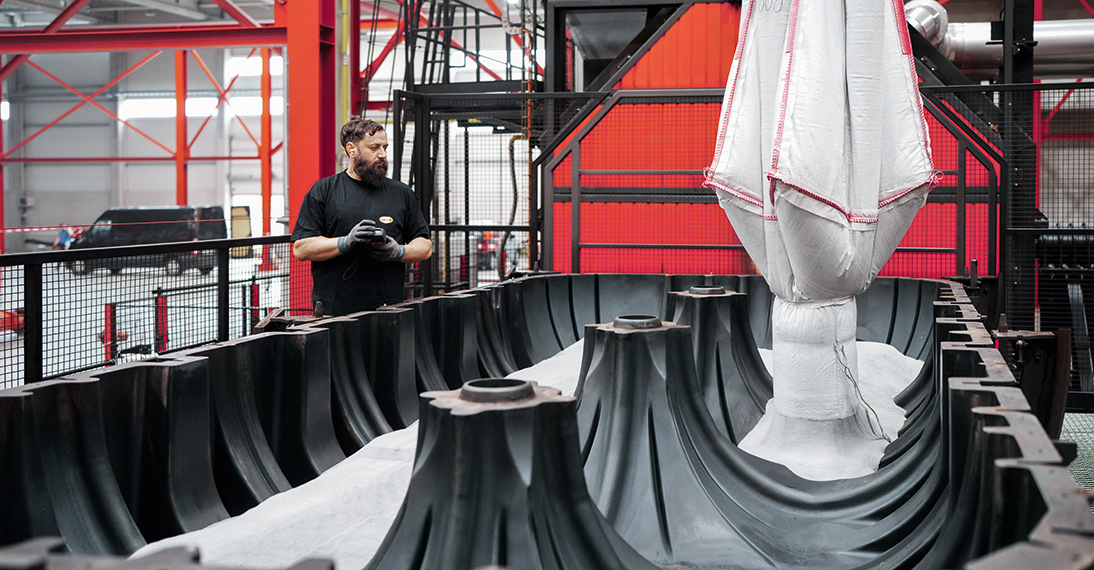
«La ventaja de este proceso es que podemos trabajar sin ningún tipo de presión y la tensión posterior en el interior del componente es extremadamente baja en comparación con todos los demás métodos de fabricación», explica nuestro experto. Esto significa que el material puede seguir procesándose sin problemas y que la durabilidad -que en el caso de los depósitos GRAF ya se prolonga durante generaciones- puede aumentar aún más. «Además, con los modernos sistemas rotativos necesitamos hasta un 90% menos de energía que con los sistemas convencionales».
En Neuried, el procesamiento posterior permite convertir los depósitos al formato XXL en caso necesario. Sin embargo, tras unos 45 a 60 minutos de «tiempo de cocción», el molde sale primero del horno y se enfría durante 100 minutos con más movimientos giratorios. A continuación, los depósitos individuales pueden ensamblarse y soldarse para formar obras de arte completas de cualquier tamaño. Unas sierras precisas cortan los extremos de los depósitos de forma totalmente automática. A continuación, los depósitos se sueldan en otros sistemas.