ELM: gli uomini di plastica
Carburante o materia prima? Il nostro partner ELM di Bissingen ha combinato entrambi i metodi di utilizzo e ha registrato un vero e proprio boom ...
Anche la bottiglia d'acqua nella sala conferenze della sede centrale del Gruppo ELM a Bissingen è etichettata a caratteri cubitali: "Riciclaggio", e sull'etichetta è raffigurato anche un ciclo. Nel caso della bottiglia d'acqua, si può ormai dare per scontato che alla fine verrà reinserita nel ciclo di riciclaggio. Questo è molto più eccitante con tanti altri prodotti in plastica che ELM ha trovato il modo di riciclare. Oggi ne scopriamo di più durante una visita allo stabilimento da parte di Matthias Einsele, che condivide la gestione e le quote dell'azienda al 50:50 con Eberhard Lebküchner. È in grado di descrivere la sua attività in modo granulare come probabilmente solo chi separa la plastica in granulometrie e frazioni specifiche per vocazione può fare.
Per cominciare: ELM è uno dei nostri partner e un fornitore di plastica riciclata di alta qualità, che viene utilizzata per realizzare cisterne per l'acqua piovana a Teningen, Herbolzheim, Neuried e Dachstein. ELM, fondata nel 1998 da Einsele, Lebküchner e Willi Männer a Bissingen, nel distretto del Baden-Württemberg di Esslingen, è oggi un gruppo di aziende con oltre 200 dipendenti e nove società in cinque sedi. I due claim "Da rifiuto a risorsa" e "Da rifiuto a combustibile" descrivono in modo appropriato le principali strade che ELM percorre con la materia prima plastica. Tutto è iniziato con il combustibile …
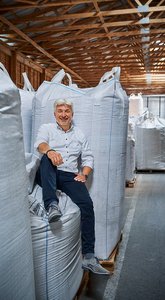
Combustibili derivati dai rifiuti (in tedesco Ersatzbrennstoffe, che abbreviato EBS)
Il signor Männer, che in precedenza aveva gestito un servizio di container puro, ha avviato la fusione di diverse aziende regionali di smaltimento dei rifiuti e ha assunto il ruolo di amministratore delegato dell'impianto di selezione che è stato poi acquisito congiuntamente dalle aziende di smaltimento dei rifiuti. Contemporaneamente, a Bissingen si liberò un magazzino tessile. I tre fondatori di Bissingen realizzarono qui la loro idea: "L'impianto di selezione dell'azienda di smaltimento dei rifiuti consentiva di separare i materiali consegnati in modo tale da poter continuare a lavorare con essi", ricorda Einsele. "Eravamo interessati alla plastica, in particolare ai materiali compositi che non potevano essere riciclati". L'azienda appena fondata li ha trasformati in combustibili sostitutivi. Le parti in plastica vengono separate dai rifiuti e modellate in modo da essere facilmente infiammabili e bruciare secondo le loro proprietà, rilasciando la massima energia possibile. Questo perché contengono molta energia e sono i cosiddetti rifiuti ad alto potere calorifico. "Questa energia deve essere utilizzata in modo sensato", concordano Einsele, Lebküchner e Männer. La parsimonia sveva, nel senso più sostenibile del termine.
L'elevato livello di energia caratterizza EBS
Possono sostituire il gas e il carbone come combustibili. Svolgono un ruolo centrale nelle calceie, nelle centrali elettriche a carbone e nella produzione di cemento, dove sono richieste ovunque temperature elevate. Alla ELM, il combustibile è destinato esclusivamente ai cementifici. La plastica brucia in enormi forni rotativi con un diametro di sei metri e garantisce la produzione di spessi mattoni di clinker sul fondo, come precursore del successivo cemento. Nessun residuo di plastica si deposita sui mattoni perché la natura bidimensionale della plastica fa sì che essa bruci completamente prima. In altre parole, le parti in plastica sono completamente appiattite. "Nel loro ambiente specifico, bruciano con meno inquinanti della polvere di carbone che sostituiscono", sottolinea Einsele. Migliorano certamente il bilancio di CO2 della produzione di cemento".
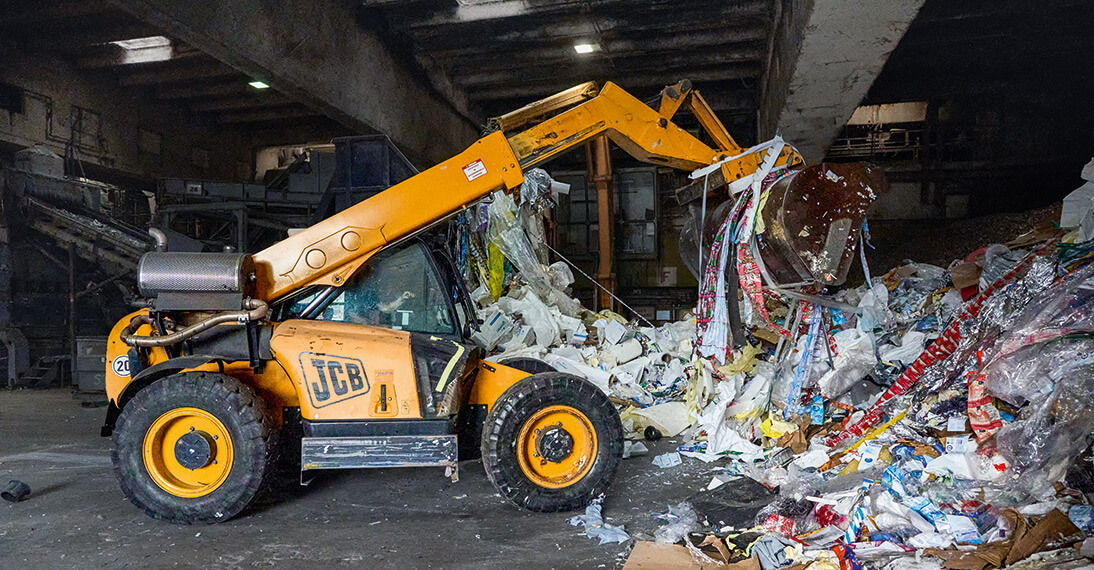
"È pura ironia che gli impianti di incenerimento dei rifiuti tedeschi non paghino ancora una tassa sulla CO2, mentre i cementifici devono farlo in tutta Europa, anche se sostituiscono il carbone polverizzato con il EBS", afferma Einsele, che conosce bene la produzione di cemento. Tanto che la ELM ha costruito i suoi impianti di Mergelstetten, Allmendingen e Harburg proprio accanto alle cementerie. "Con le grandi quantità che forniamo ai nostri clienti a lungo termine e adattate alla rispettiva produzione, ha senso farlo solo in questo modo", dice Einsele. "Nel 1998 abbiamo detto che se fossimo riusciti a produrre 12.000 tonnellate di EBS all'anno, saremmo stati felici. Ora sono quasi 300.000 tonnellate all'anno!".
Nel 2011, ELM ha chiuso il cerchio e ha aperto un secondo percorso.
Da rifiuto a risorsa, a materia prima. La parola magica è: riciclo dei materiali. Grazie al miglioramento dei processi, ELM era ora in grado di separare la plastica del suo EBS in frazioni sempre più fini. Allo stesso tempo, questo ha avuto il vantaggio di rendere il combustibile sostitutivo più reattivo, cioè più facile da incendiare. Per l'elevato tasso di utilizzo del suo combustibile sostitutivo, che raggiunge il 100% nel bruciatore del cementificio, ELM ha ricevuto anche il certificato di una delle 100 aziende più efficienti dal punto di vista delle risorse nel Baden-Württemberg nel 2017.
Grazie alla nuova separazione dei materiali, le parti in plastica dura più grandi sono state lasciate in sospeso.
Dove metterlo? Con la nostra indagine, ELM ha trovato una risposta chiara: di nuovo nel ciclo! Ne siamo stati entusiasti, perché siamo sempre alla ricerca di nuove fonti di materie prime. ELM ha adattato il suo sistema di selezione alle nostre esigenze e così abbiamo promosso il nuovo ramo del gruppo ELM: "In collaborazione con GRAF, abbiamo impostato il nostro sistema di separazione in modo tale da separare in modo affidabile le poliolefine, note anche come PO, che sono preziose per GRAF". Le parti di plastica pre-tritate vengono separate in una sorta di piscina utilizzando la tecnologia del galleggiamento, spiega ancora Einsele. Segue la post-pulizia, che include la rimozione delle fibre miste, e infine il confezionamento dei fiocchi di PO finiti in grandi sacchi. Nel padiglione 2, che Einsele ci sta mostrando, oltre ai consueti big bag per la consegna viene ora utilizzato anche un semirimorchio per autocarri con una capacità di oltre 90 metri cubi.
"GRAF è uno dei pochi produttori che si impegna a sostituire la plastica primaria con i riciclati. Anche al culmine della pandemia, GRAF ha continuato a ordinare da noi e ora abbiamo fornito a GRAF un totale di oltre 16.000 tonnellate di scaglie di PO. La plastica primaria è attualmente troppo economica, ed è proprio per questo che partnership come quella con GRAF sono così cruciali".
L'ELM continuerà a crescere nel riciclaggio nel medio-lungo termine.
"Nel settore del EBS, abbiamo già quasi coperto il consumo di carburante dei nostri clienti. Il percorso 'da rifiuto a risorsa' non è solo una questione di convinzione per noi, ma anche di vendite", afferma Einsele. Per inciso, la spettroscopia nel vicino infrarosso (NIR) viene utilizzata anche per separare le preziose plastiche riciclate. È la stessa tecnologia che successivamente separa le poliolefine in PE e PP.