Farmer looking for plastic
Farmer, inventor, cleaner: Bernhard Wilken is as versatile as his Emsland-based company. And it's not just a chicken farm, but also an important part of our GRAF recycling cycle. Find out in the following report what measures Wilken is already taking in the area of sustainability and how they are working with us:
If there's one thing that drives the boss up the wall, it's wasting energy. "Oh, Mr. Wilken doesn't like that at all!" an employee confirms behind closed doors. But he is right: "Everyone is talking about sustainability, but for us, closed cycles have always been part of it," he adds. And so the family farm in Haren not only uses its own biogas plant to generate its own energy, but also uses the residual heat from it for the henhouse and to dry washed plastic - which is then later recycled. And the poultry don't just get anything to peck at, but organic feed from their own fields - while the manure ends up in the biogas plant. The cycle à la Wilken. How exactly does this relate to agriculture and plastic? It's best to start the story from the beginning ...
The history of the Wilken company
We are in Emsland, just a stone's throw from the Dutch border. On a piece of land that at first glance, with its lush greenery, seems not only charming but also incredibly vast. Northern Germany, after all. The spring wheat rustles in the wind in front of the Wilkens' farm. Clouds are gathering from the west, promising rain, but not actually bringing any. "That's a shame," says Bernhard Wilken as he shows us around his farm later on. "We could really do with it to keep everything here as green as it is." Nevertheless, the farm horses have taken the precaution of moving into their stables.
The family farm, founded by Grandpa Wilken in 1931, has been a cornerstone of the region ever since. Bernhard's father continued farming as his main occupation. However, his son, who has always been a technology enthusiast, decided to train as a farmer, work part-time and complete an additional apprenticeship as a construction mechanic. This is fortunate when you look back and see what the farm, where the next Wilken generation is already helping out with son Henrik, has become as the nucleus of the Wilken Group. Bernhard Wilken's dexterity and his understanding of machines and mechanics have allowed the family business to grow considerably.
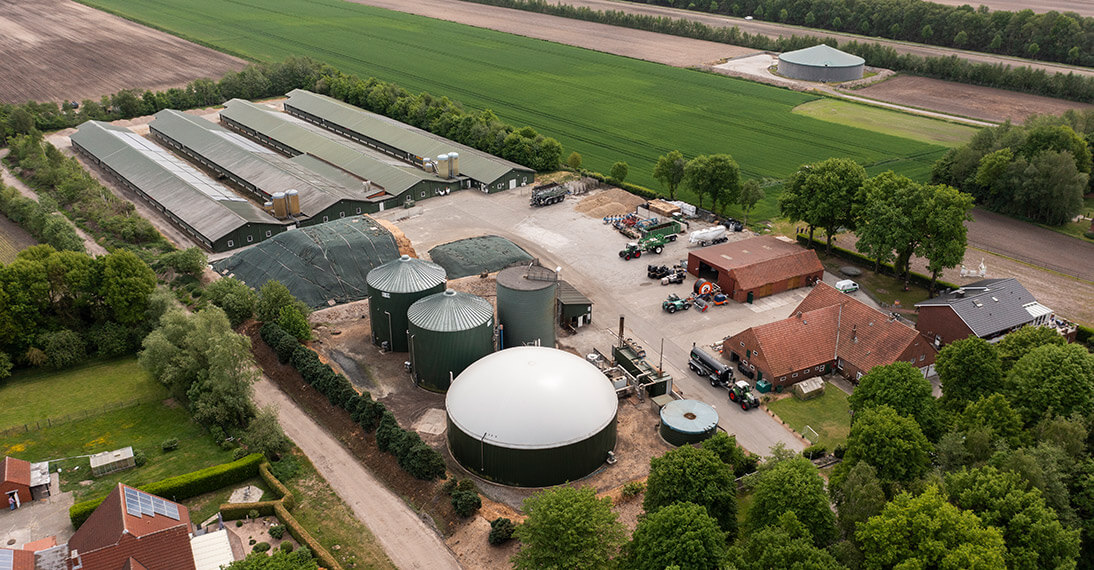
He now employs 65 people. Of these, 45 at Wilken Plastics Energy are responsible for shredding, washing and sorting the plastic waste that is delivered. From here, a large proportion of the plastic waste is then sent to our Raw Materials Competence Center in Herbolzheim, where it is processed into recyclates and reused - for long-lasting solutions in the important field of rainwater management. This takes sustainability a step further - right through to the finished product.
Shredding, washing, drying
"In principle, the processes involved in plastic washing are the same as those used in animal feed production," says Wilken, answering the obvious question of how such an idea could even come about. And as matter of fact as they are, the people from this particular region, who have somehow always been dependent on good ideas due to their remoteness. "It was obvious to me, and I was also annoyed at the time that we could only use the residual heat from our biogas plant to heat the chicken coops in winter," says the entrepreneur.
In summer, it simply fizzled out. In the meantime, a six-kilometer-long pipe feeds the biogas under the family's fields into a combined heat and power plant at the washing and sorting facility, which Bernhard Wilken planned and developed himself a good 15 years ago. There, the gas is converted into bio-electricity and bio-heat. "Nothing is wasted here anymore. Everything is connected," says Wilken. With a good six million kilowatt hours of electricity, there is even some left over for neighboring farmers.
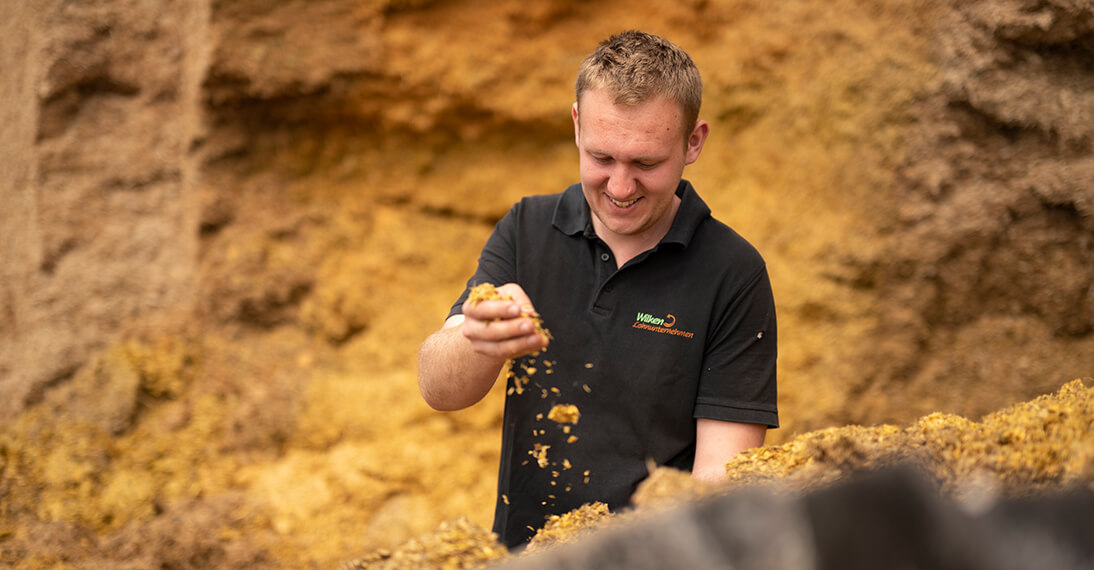
Wilken's contribution to climate protection
The family business produces the energy it needs completely independently. And on top of that, the company also makes a significant contribution to climate protection: the process saves the CO2 consumption of 1,300 cars a year. "These are the connections that we should all be paying more attention to in these times," says the boss. "After all, nothing is wasted in nature."
We drive over to the plastics processing plant with Bernhard Wilken. In an electric Audi, of course, if you have your own electricity at home. Six kilometers from the yard, right next to the freeway, we finally recognize the Wilken logo at the gate. In the yard, a truck is being loaded with freshly washed, shredded plastic. It can hold 25 tons. Four such trucks leave the factory premises almost every day. This means that 35,000 tons of recycled material are processed at Wilken Plastics every year. Speaking of processing: this is also done with the water used to wash the plastic. The dirty liquid is passed through a special filter system, collected and clarified. A cycle, what else!
»Nothing is wasted here, everything is connected. This is how we manage to clean the plastics as sustainably as possible«
The delivered plastic waste is piled up meters high around the old factory building - ready to be shredded, washed and sorted. However, it doesn't lie around here for long. The hall roars accordingly. The machines are running at full capacity. After all, there is plenty to do. The demand for the processed and pre-sorted recycling material is huge. Right next door, Bernhard Wilken is therefore already building a new, even larger plant with even more powerful and efficient machines. Once again, many of the ideas for this come from the boss himself. He is investing 10 million euros in it. Investing in sustainability was the right thing to do 15 years ago - and even more so now, says the inventor from Emsland.
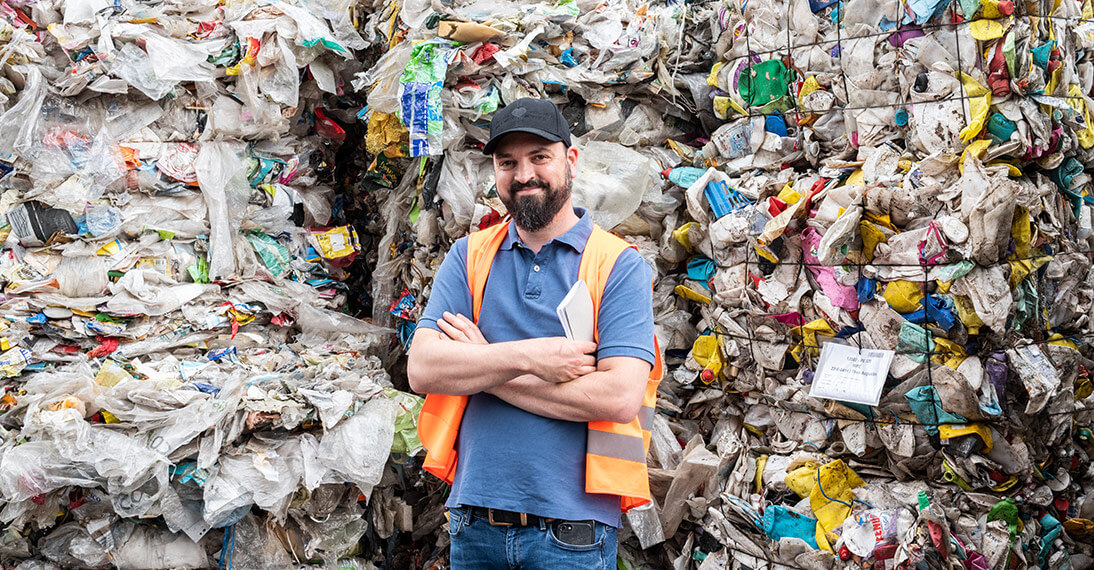
The wheel loader tips the plastic waste into a hopper virtually every minute. It then goes into the sorting systems, which Bernhard Wilken largely co-developed, where the plastics are pre-sorted. How do the machines work in detail? "That remains our company secret, of course," says Bernhard Wilken, grinning mischievously. Something about circulation. That much we have understood in any case...