The Musclemen of Plastic
Fuel versus raw material? Our partner, ELM in Bissingen, has ingeniously combined both recycling methods – and the results have been remarkable.
Even the water bottle in the ELM Group's conference room at its headquarters in Bissingen boldly bears the label "Recycling", with a cycle depicted alongside. While it's now commonplace for water bottles to find their way back into the recycling loop, the same can't always be said for many other plastic products that ELM has found innovative ways to recycle. During a recent factory tour led by Matthias Einsele, who co-manages the company 50:50 with Eberhard Lebküchner, we gained deeper insights into their operations. He is able to describe his business as granularly as probably only someone who separates plastics into specific grain sizes and fractions by vocation can.
To start with, ELM is one of our partners and a supplier of high-quality recycled plastic used to make rainwater tanks in Teningen, Herbolzheim, Neuried and Dachstein. ELM, founded in 1998 by Einsele, Lebküchner and Willi Männer in Bissingen an der Teck in the Baden-Württemberg district of Esslingen, is now a group of companies with more than 200 employees and nine companies across five locations. The two claims "From waste to resource" and "From waste to fuel" aptly describe the main paths ELM takes with the raw material plastic. And it all began with fuel ...
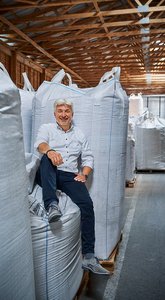
Refuse-derived fuels, or RDF for short
Mr. Männer, who previously managed a pure container service, initiated the merger of several regional waste disposal companies and took on the role of managing director of the sorting plant that was then jointly acquired by the waste disposal companies. At the same time, a textile warehouse became vacant in Bissingen. And the three Bissingen founders put their idea into practice here: "The waste disposal company's sorting plant now made it possible to separate the delivered materials so that we could continue working with them," recalls Einsele. "We were interested in the plastic - and in particular the plastic composites that could not be recycled." The newly founded company turned this into substitute fuels. The plastic parts are separated from the waste and shaped in such a way that they are easily flammable and burn according to their properties, releasing as much energy as possible. This is because they contain a lot of energy and are so-called high-calorific waste. "This energy has to be put to good use," Einsele, Lebküchner and the men agreed. Swabian thriftiness - in the most sustainable sense.
The high level of energy characterizes RDF
They can replace gas and coal as fuels. They play a central role in lime works, coal-fired power stations and in the production of cement, where high temperatures are required everywhere. At ELM, the fuel goes exclusively to cement works. The plastic burns in huge rotary kilns with a diameter of six meters and ensures that thick clinker bricks are produced at the bottom as a preliminary stage of the later cement. No plastic residue is deposited on the bricks because the two-dimensional nature of the plastic means that it burns completely beforehand. In other words, the plastic parts are completely flattened. "In their specific environment, they burn with fewer pollutants than the coal dust they replace," emphasizes Einsele. They certainly improve the carbon footprint of cement production.
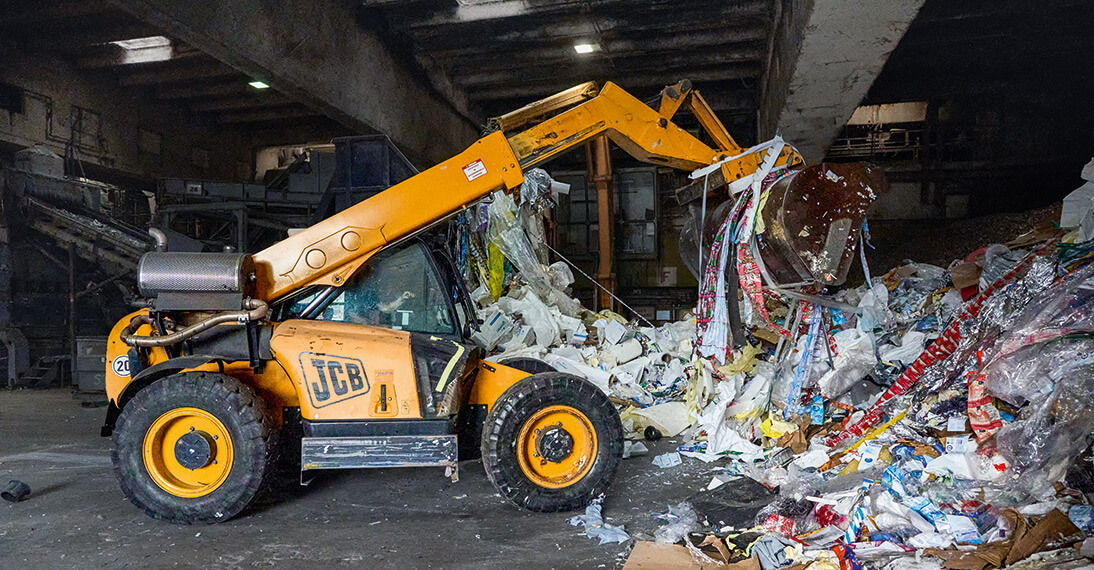
"It's pure irony that German waste incineration plants still don't pay a CO2 tax, but cement plants have to do so throughout Europe, even if they replace pulverized coal with RDF," says Einsele, who is well versed in cement production. Hence, ELM has built its plants in Mergelstetten, Allmendingen and Harburg right next to the cement plants there. "With the large quantities that we supply to our customers on a long-term basis and adapted to the respective production, it only makes sense to do it this way," says Einsele. "In 1998, we said that if we could produce 12,000 tons of RDF a year, we'd be happy. Now it's almost 300,000 tons per year!"
In 2011, ELM completed the loop, embarking on the second recycling avenue: from waste back to resource, to raw material.
The magic word is: material recycling. Thanks to improved processes, ELM was now able to separate the plastics in its RDF into ever finer fractions. At the same time, this had the advantage of making the substitute fuel more reactive, i.e. easier to ignite. In 2017, ELM received the certificate as one of the 100 most resource-efficient companies in Baden-Württemberg for the high use rate of up to 100 percent of its substitute fuel at the cement plant's burner.
Thanks to the new material separation, the larger hard plastic parts were now left over
What to do with them? With our inquiry, ELM found a clear answer: back into the cycle! We were delighted, as we are constantly on the lookout for new sources of raw materials. ELM adapted its sorting system to our needs accordingly and so we promoted the new branch of the ELM group of companies: "In cooperation with GRAF, we have set up our separation system in such a way that the polyolefins, also known as POs, which are valuable for GRAF, are reliably separated." Using float-sink technology, the pre-shredded plastic parts are separated in a kind of swimming pool, Einsele explains further. This is followed by post-cleaning, including the removal of added fibers, and finally the packaging of the finished PO flakes in big bags. In Hall 2, which Einsele is now showing us, a semi-trailer truck with a capacity of more than 90 cubic meters is now used in addition to the usual big bags for product delivery.
"GRAF is one of the few manufacturers that is fully committed to replacing primary plastics with recyclates. Even at the height of the pandemic, GRAF continued to order from us, and we have now supplied GRAF with a total of more than 16,000 tons of PO flakes. Primary plastics are currently far too cheap, which is precisely why partnerships like the one with GRAF are so crucial."
ELM will continue to grow in recycling in the medium to long term
"In the RDF sector, we've nearly met our customers' fuel demands. The path 'from waste to resource' is not just a question of conviction for us, but it’s also a sales imperative," says Einsele. Incidentally, near-infrared spectroscopy (NIR) is also used to separate the valuable recycled plastics. This is the same technology that later separates the polyolefins into PE and PP.