Record-Breaking: Our XXL Rainwater Tanks
Up to 13 meters long with a volume of a whopping 52,000 liters: The really big things are made at our newest plant in Neuried. Plant manager Heiko Rapp takes us inside the production facility and explains how the XXL rainwater tanks are actually made ...
So let's go! But where do we actually start? Heiko Rapp takes us outside, where a truck has just arrived from nearby Herbolzheim. There, at the GRAF Raw Materials Competence Center, plastics are recycled from waste, such as yellow bags for example.
They arrive in Neuried and the other GRAF production sites in Teningen and Dachstein as granulate and are first conveyed into huge silos. But before the high-quality plastics can be shaped, they have to be ground into powder in a huge mill.
The energy for production comes from largely sustainable sources, explains Heiko Rapp. There is a huge photovoltaic system on the roof, for example, which alone covers 70 percent of the electricity requirements, and even 100 percent during the day.
But now we're back to our tank and our little tour. A new mold for a platin flat tank is being filled with the plastic powder. “You can imagine it's a bit like a giant cake tin,” explains Heiko Rapp. Conveniently, the oven in which the finally closed shell is then placed is already preheated. At 300 degrees, the plastic inside the mold is finally melted and distributed particularly evenly by the slow rotational movements of the machine. The outer wall of the tank builds up on the inner wall of the mold.
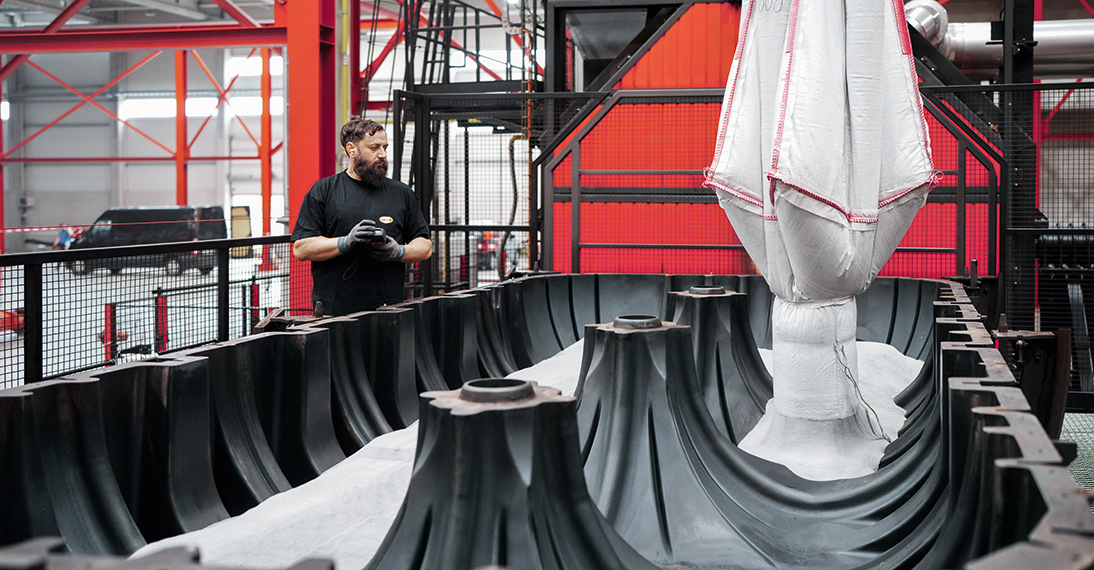
“The advantage of this process is that we can work without any kind of pressure and the subsequent tension inside the component is extremely low compared to all other manufacturing methods,” explains our expert. This means that the material can then be further processed without any problems and the durability - which in the case of GRAF tanks already extends over generations - can be further increased. “We also need up to 90 percent less energy with the modern rotary systems compared to conventional systems.”
In Neuried, further processing means that the tanks can then be converted to XXL format if required. After around 45 to 60 minutes of “baking time”, however, the mold first leaves the oven and cools down for 100 minutes with further rotational movements. The individual tanks can then be fully assembled and welded together to form complete works of art of any size. Precise saws cut off the tank ends again fully automatically. The tanks are then welded together in further systems.